Long Belt Grinding Machines are essential industrial tools renowned for their ability to achieve high-quality surface finishing, material removal, and shaping across various materials and industries. Unlike smaller belt sanders, these machines utilize a significantly longer abrasive belt, offering distinct advantages, particularly for large or complex workpieces.
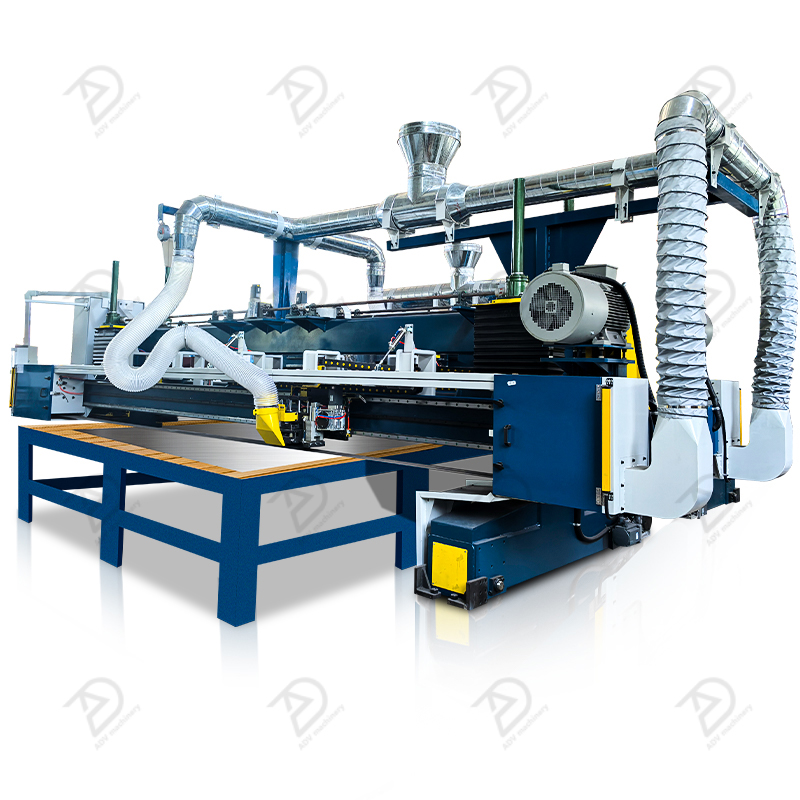
What is a Long Belt Grinding Machine?
At its core, a Long Belt Grinding Machine employs a continuous abrasive belt that runs over a drive wheel and an idler wheel. The workpiece is brought into contact with the moving belt, often supported by a platen or contact wheel, to perform grinding, polishing, or material removal operations. This design allows for consistent and efficient processing of large surface areas.
Key Applications Across Industries
The versatility of Long Belt Grinding Machines makes them indispensable in a wide array of sectors:
- Metal Fabrication and Sheet Metal Processing: They are widely used for deburring, removing scale, and achieving desired surface finishes on sheets, plates, and fabricated components. They are also highly effective for dressing weld seams, improving both the appearance and structural integrity of welded joints.
- Heavy Machinery and Foundries: These machines are crucial for removing casting imperfections like burrs, gates, and risers from large castings and heavy machinery parts, ensuring smooth and functional surfaces.
- Automotive and Aerospace: Precision grinding of critical components in the automotive and aerospace industries is a key application, where tight tolerances and specific surface characteristics are paramount.
- Surface Preparation: Long belt grinding is often a prerequisite for subsequent processes such as welding, rolling, explosion cladding, or applying protective coatings. It prepares surfaces for optimal adhesion and functional performance.
- Creating Special Surfaces: They can be used to create specific surface textures, such as anti-slip surfaces with a cross-grain pattern, or decorative finishes on various metals including steel, aluminum, stainless steel, titanium, and copper.
- Other Applications: Their use extends to knife making, tool sharpening, and even in the production of musical instruments and for restoration purposes.
Advantages of Using Long Belt Grinding Machines
Long Belt Grinding Machines offer several significant benefits that contribute to their widespread adoption:
- High-Quality Surface Finish: They are capable of producing exceptionally smooth, consistent, and specific surface finishes, even on large, wavy, or irregularly shaped blanks with cutouts.
- Efficient Material Removal: With powerful drive units and high belt speeds (up to 25 m/s), these machines can achieve high material removal rates while maintaining consistent quality.
- Reduced Heat Influence: The longer belt facilitates better heat dissipation, minimizing the thermal impact on the workpiece surface. This low heat influence is crucial for subsequent processes like welding and surface protection, often eliminating the need for additional preparation.
- Processing Large Workpieces: Designed with large working areas, many models can machine oversized workpieces in a single operation, reducing setup time and increasing efficiency.
- Versatility in Materials and Operations: They can effectively process a wide range of materials and perform various tasks from aggressive grinding to fine polishing.
- User-Friendly Operation: Modern machines often feature intuitive control systems (like S7 with OP-Panel) that make programming and setup of parameters like dimensions, speeds, and pressure straightforward. Handheld pendants can further assist in setup and teaching new programs.
- Quick Belt Change: Features like self-centering belt run facilitate quick and simple changes of the grinding belt, minimizing downtime.
- Improved Workshop Safety and Layout: Options like track guiding embedded in the floor can create a smooth, even surface, reducing trip hazards for operators and vehicles.
Types and Configurations
Long Belt Grinding Machines come in various configurations to meet specific needs:
- Fixed or Movable Frame: The machine frame can be fixed, with the workpiece moving, or movable, with the grinding unit traversing a stationary workpiece, ideal for very large items.
- Single or Multiple Grinding Units: Machines can be equipped with one or two (or more) belt grinding units, allowing for different grits or sequential operations.
- Automation Levels: From manual operation to fully automated CNC systems, the level of automation can be tailored to production requirements.
- Specialized Designs: This includes portal grinding machines for oversized plates and conveyorized systems for high-efficiency automated processing.
Key Considerations for Selection
When choosing a Long Belt Grinding Machine, several factors are crucial:
- Motor Power and Belt Speed: These must match the intended materials and desired removal rates.
- Belt Dimensions: The width and length of the belt influence processing area, belt life, and power requirements.
- Frame Construction: A robust frame is essential for stability, precision, and durability.
- Safety Features: Adequate guarding, dust extraction, and emergency stops are paramount.
- Automation and Control: The level of automation should align with production volume and precision needs.
In conclusion, Long Belt Grinding Machines are powerful, versatile, and efficient tools that play a vital role in modern manufacturing and fabrication. Their ability to handle large workpieces, deliver high-quality finishes, and adapt to various applications makes them a valuable investment for industries requiring precise surface processing.